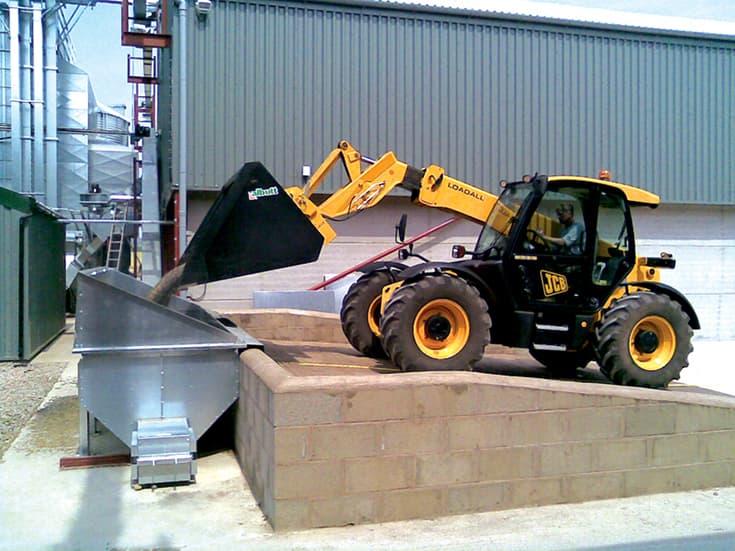
Perry of Oakley is a family run business and they have been manufacturing conveying equipment and driers for over seventy years. This article has been written to help you select thr right sort of grain intake for your application.
Selecting an intake pit
When considering which type of mechanical intake system to use the first thing to consider is the type of products to be handled. If the products are all free flowing such as cereals then a chain and flight conveyor system will be suitable. If the products also include meals and very light products these might not be suitable for a chain and flight conveyor and then a more universal screw conveyor system may be the answer
This is because chain and flight conveyor systems generally use a side inlet configuration to enable control of the depth of the product in the conveyor casing. This can lead to a narrow aperture for the product to pass through and this does not suit products that are likely to bridge.
Other considerations are that a screw conveyor intake would generally be shorter as it is not good practice to have a hanger bearing to support the worm on pipe inside the hopper area. This can be achieved but access for regular lubrication also has to be considered.
Intake hoppers using chain and flight conveyors offer several benefits:
Types available:
Screw conveyor - Horizontal chain and flight conveyor - Curved chain and flight conveyor
- The intake section can be very long. Perry systems have intake sections from 3m to 18m depending on the model of the conveyors.
- The chain and flight conveyors after the intake section can be any length required.
- The chain and flight conveyors can be curved, depending on the storage volume requirements this could mean the civil works for intake pits can be very simple and can even be a flat pad if needed.
Capacity of intake pits
This will depend on a number of factors:
- The capacity of the equipment following the intake may limit the chosen capacity.
- What rate does the rest of the system need to be fed at? For example if the intake is part of a drying system then depending on the configuration of this the general rule of thumb is that the handling equipment should be twice the normal drying capacity of the drier.
- If not then the daily intake capacity needs to be known.
- The arrival interval of delivery vehicles
- The acceptable waiting time for the delivery vehicles and space for them to wait without causing problems with local roads.
- If delivery vehicles need to be emptied quickly but the interval is not that frequent could the intake pit be down below ground a suitable distance to allow the contents of the trailer to be tipped and instantaneously disappear below ground level. The conveyor can then empty this before the next vehicle arrives.
Delivery vehicle considerations
- Is it a single bulk truck with a large trailer which is hydraulically tipped. This could use a short intake pit and reverse up to it or drive over it.
- A shorter bulk truck towing a smaller bulk trailer. For faster unloading this requires a drive over pit so the truck can tip first and then pull forward over the pit and then tip up the trailer.
- A long bulk trailer with bottom emptying hoppers. This would suit a drive over pit and then the truck empties each compartment in turn when in the correct position over the pit or if faster discharge is required a long intake pit for the full length of the truck so all compartments can be opened at the same time.
- Truck with side tipping trailer or hydraulic truck tipping platform. This would need a long intake pit parallel to the truck position the same length of the truck.
- Is the pit to be large to enable a wet pre store of grain to be held before drying instead of the expense of a wet storage bin. In this case a long intake pit is useful to enable a large volume of grain to be heaped above the intake pit with surrounding walls. The delivery trucks can reverse up to the pit along it’s length and tip up at different points along it.
- Layout of the intake system, For instance is the pit to be reversed up to or is it to have a drive over grid. If a drive over configuration will the conveyor be perpendicular to the direction of the truck or parallel to it. If it is perpendicular to it, then the positioning of the next piece of equipment can easily be positioned out of the way of the delivery vehicle route. If it is parallel and a drive over configuration then a second conveyor will be needed to connect the intake conveyor to the elevator to keep out of the way of the truck route.
How deep should the pit be?
This may be determined by the local ground water conditions. If there is a very high water table then the pit may be shallow or even positioned above ground for vehicles to reverse up to it or to pull alongside it if side tipping.
Most pits are of a suitable capacity and are positioned just below floor level so a run over grid can be installed over the top.
Alternatively the intake conveyor can be positioned deep down at the bottom of a large gravity pit if the water table permits.
The most popular configuration of intake conveyor that Perry manufacture has an average length of 6m and has a 45 degree curve at the outlet end to feed into a belt and bucket elevator or aspirator cleaner. Typical capacities from 60 to 300tph, but capacities are available up to 800tph.
Perry’s manufacture two types of intake hopper for chain and flight conveyors. A trench intake and a mechanical reception hopper.
The mechanical reception hopper is supplied as a complete hopper in standard sections of 3, 4.5 or 6m (longer on industrial conveyors) and multiple units can be fitted to a single conveyor. The flow rate is controlled by a pair of vertical slides in the hopper which are controlled by levers at the outside of the hopper so no inverter control is necessary.
The second type is a trench intake, this comes with or without a pre-assembled hopper and in multiple smaller sections and these can be assembled on site to create single intakes up to 18m long. These have a fixed side inlet aperture and so the speed of the conveyor needs to be inverter controlled to control the flow rate of the grain into the rest of the equipment.
Both systems can have extension hoppers manufactured at the factory or on site to extend the hoppers to the required dimensions.
Perry of Oakley Ltd's screw conveyor intakes are tailor made to suit customer requirements and products and have diameters from 150 to 600mm. To control the fed rate on these inverter control is required.
Perry of Oakley Ltd are the UK’s most experienced manufacturer of materials handling & drying equipment. Established in 1947, last year saw the third generation, family run firm turn 70. Everything Perry of Oakley Ltd sell is designed and manufactured in house and they have a network of UK and international dealers and engineers